En las condiciones de desarrollo dinámico de los procesos de la economía moderna, la creación de industrias y procedimientos de control cada vez más complejos, uno de los enfoques más relevantes para su mejora es la introducción de métodos para optimizar diversas pérdidas. En primer lugar, esto se refiere a los recursos de las empresas: temporales, financieros, tecnológicos, energéticos y otros.
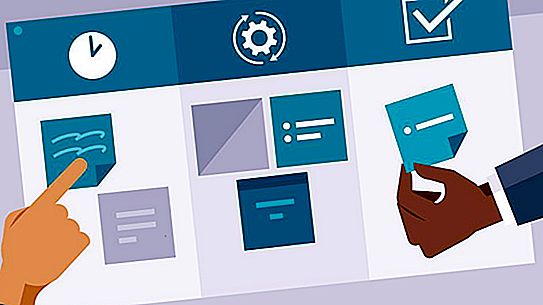
Características de la actividad.
En la práctica, hay un cierto límite, que está asociado con el nivel de desarrollo tecnológico y organizacional del sistema (organización, empresa). Está claro que no es práctico exigir la automatización total de la producción de un pequeño taller para coser ropa según diversos criterios, y especialmente económicos. Sin embargo, independientemente del tamaño del sistema, es necesario garantizar el uso máximo y óptimo de los recursos disponibles con pérdidas mínimas, lo cual es cierto para cualquier organización y actividad.
En este caso, se hace necesario utilizar técnicas de control de proceso progresivo que se basen en la teoría de crear producción ajustada o ajustada. Estos incluyen sistemas 5S y TPM, mapeo de flujo de valor y SMED, etc.
Propósito de innovación
La producción ajustada ("ajustada") es un sistema de enfoques especiales para organizar actividades, que considera su objetivo principal de eliminar las pérdidas de una naturaleza diferente en el sistema. El mecanismo es bastante simple: todo lo que no agrega valor al cliente debe clasificarse como innecesario (pérdida) y eliminarse del sistema. Está claro que la piedra angular es el concepto de "pérdida", ya que su definición afectará directamente la efectividad del método. En este caso, la capacitación en el mapeo del flujo de creación de valor para sus especialistas es una ventaja significativa en el mercado para la prestación de servicios.
Tipos de perdidas
Lean Manufacturing es uno de los conceptos fundamentales de la logística de fabricación. Y aunque existen varios enfoques diferentes para determinar las pérdidas, destacamos los tipos más universales:
- Tiempo de espera: cualquier tiempo de inactividad en la actividad reduce el valor del producto final. La espera de materiales, reparaciones de equipos, información u orientación de la gerencia ralentiza el proceso y aumenta el costo de su implementación.
- Operaciones innecesarias (procesamiento innecesario de productos): operaciones tecnológicas innecesarias, etapas de proyectos, todo lo que proporcionan los procedimientos estándar, pero puede nivelarse sin perder la confianza del cliente.
- Movimiento innecesario de trabajadores: la búsqueda de herramientas, equipos, movimientos irracionales debido a la mala organización del lugar de trabajo, etc.
- Movimiento innecesario de materiales: mala organización del sistema de inventario, falta de logística de transporte progresiva y mecanismos de subcontratación para el suministro de material y técnico.
- Exceso de existencias: la vinculación del capital de trabajo de la organización como resultado de los altos costos del exceso de posiciones en el almacén.
- Pérdidas tecnológicas: sistemas de procesamiento de datos obsoletos, procesos tecnológicos y rutas de procesamiento.
- Pérdidas por sobreproducción: la fabricación de cantidades excesivas de productos, lo que conduce a un aumento en el costo de almacenamiento, transporte y posterior venta.
- Pérdidas intelectuales: la falta de mecanismos para alentar la iniciativa de los trabajadores y empleados, un sistema débil de propuestas de racionalización, la supresión de un enfoque creativo del trabajo.
Uno de los métodos más comunes para eliminar pérdidas en el sistema y optimizar los procesos de implementación del proyecto es mapear el flujo de valor. Lean Manufacturing le permite crear un sistema adaptativo que responde de manera flexible a los cambios en el entorno.
Flujo de valor
Un flujo de valor es un conjunto de todas las acciones (operaciones) que se realizan en un producto para lograr el estado deseado u obtener las características requeridas. Las acciones se diferencian en dos grupos:
- crear valor del producto (agregar valor);
- no creando valor de producto.
Como se puede ver en la figura presentada, las etapas de cambio tecnológico del producto (color azul) agregan valor al producto, y las etapas de las operaciones auxiliares - preparatoria, transporte, almacenamiento - (color rosa) - por el contrario, reducen el valor del producto debido a la pérdida innecesaria de tiempo.
Proceso de mapeo
La base de la técnica de mapeo es el desarrollo de un algoritmo gráfico especial que muestra el proceso de creación de productos (ejecución del proyecto) a lo largo del tiempo. Este algoritmo se denomina mapa de flujo de valor, que es un modelo gráfico basado en un conjunto específico de caracteres (signos, símbolos).
Las principales ventajas de la tarjeta:
- obtener un modelo gráfico del proceso en curso, teniendo en cuenta varios procesos adicionales para una percepción visual holística (la tarea es ver el flujo general de eventos);
- la capacidad de detectar varios tipos de pérdidas en todas las etapas del proyecto;
- la posibilidad de optimización paramétrica del modelo resultante para minimizar costos de todo tipo;
- trabajamos con varios indicadores del algoritmo, que encontrarán expresión en la mejora de procesos reales.
Formación del mapeo del flujo de valor basado en gráficos y símbolos estándar: bloques rectangulares y triangulares, flechas direccionales y escalonadas y otras formas. Permite registrar las etapas del proceso en estudio en un lenguaje común a todos los especialistas. Al mismo tiempo, se recomienda diferenciar los símbolos según el flujo en cuestión: material o informativo.
Los mecanismos para mapear el flujo de creación de valor en la fabricación ajustada nos permiten identificar todos los lugares de acumulación de elementos innecesarios.
Reglas de construcción
El mapeo del flujo de creación de valor implica la implementación de una serie de pasos simples que le permitirán crear rápidamente el modelo de proyecto deseado con los parámetros especificados. Por ejemplo:
- Analizar los flujos de material e información para obtener una imagen confiable del estado actual del proceso.
- Pass fluye en las direcciones hacia adelante y hacia atrás para identificar las causas ocultas de las pérdidas y encontrar patrones negativos.
- Bajo cualquier circunstancia, tome medidas de tiempo usted mismo, sin depender de los resultados de otros especialistas o valores estándar.
- Si es posible, cree un mapa también por su cuenta, lo que permitirá evitar tanto los errores de los demás como las soluciones de plantilla.
- Concéntrese en el producto en sí, no en las acciones de los operadores o equipos.
- Construye un mapa manualmente usando un lápiz o marcadores.
- Visualice elementos de proceso con colores para mejorar la percepción.
Ejemplos de asignación de flujo de valor
Considere el ejemplo de crear un mapa de flujo en el campo del flujo de trabajo inherente a las actividades de cualquier institución.
La tarea principal es elegir el mejor proveedor. El proceso de decisión estándar es el siguiente: selección del proveedor (12 días) - ejecución del texto del contrato (3 días) - aprobación por los servicios funcionales (18 días) - visa de la persona autorizada (3 días) - obtención del sello del jefe (1 día) - obtención de la firma de la contraparte (7 días) - registro en las autoridades (3 días).
Total, obtenemos el tiempo necesario para obtener el contrato requerido: 48 días. El resultado del análisis fue el descubrimiento de los cuellos de botella del esquema de toma de decisiones.
Los principales cambios después de analizar el mapa:
- Se emitió una orden para delegar la firma de parte de los documentos a los jefes de departamento (reduciendo la carga en el aparato de control y reduciendo significativamente el número de aprobaciones).
- Se han desarrollado los mismos requisitos para todos los servicios (una comprensión común de los requisitos para los documentos del contrato, reduciendo el número de errores de los artistas intérpretes o ejecutantes)
- Implementó el principio transversal de analizar la documentación mediante la creación de un grupo común de especialistas de diferentes servicios.
- Nuevas plantillas de contrato utilizadas.
- Mecanismos de documentación optimizados a través de un sistema electrónico.
- Se ha desarrollado un sistema electrónico para rastrear la calidad de los documentos que pasan por las etapas del proceso.
El principal resultado del mapeo del flujo de creación de valor fue una reducción de 2 veces en el tiempo necesario para obtener la documentación contractual, incluido el tiempo de coordinación en los servicios departamentales.